Francúzsky inštitút solárnej energie INES vyvinul nové PV moduly s termoplastmi a prírodnými vláknami pochádzajúcimi v Európe, ako je ľan a čadič. Cieľom vedcov je znížiť environmentálnu stopu a hmotnosť solárnych panelov a zároveň zlepšiť recykláciu.
Recyklovaný sklenený panel na prednej strane a ľanový kompozit na zadnej strane
Obrázok: GD
Z časopisu PV France
Vedci z francúzskeho Národného inštitútu Solar Energy Institute (INES)-divízia francúzskej alternatívnej energie a komisie pre atómovú energiu (CEA)-vyvíjajú solárne moduly s novými biologickými materiálmi na prednej a zadnej strane.
„Keďže uhlíková stopa a analýza životného cyklu sa teraz stali nevyhnutnými kritériami pri výbere fotovoltaických panelov, získavanie materiálov sa v nasledujúcich rokoch stane zásadným prvkom v Európe,“ uviedol Anis Fouini, riaditeľ CEA-Fores. , v rozhovore pre PV Magazine France.
Aude Derrier, koordinátorka výskumného projektu, uviedla, že jej kolegovia sa zaoberali rôznymi materiálmi, ktoré už existujú, aby našli tie, ktoré by mohli výrobcom modulov produkovať panely, ktoré zlepšujú výkon, trvanlivosť a náklady a zároveň znížia vplyv na životné prostredie. Prvý demonštrant pozostáva z heterojunkčných (HTJ) solárnych článkov integrovaných do celkového materiálu.
"Predná strana je vyrobená z polyméru naplneného zo sklenených vlákien, ktorý poskytuje priehľadnosť," uviedol Derrier. „Zadná strana je vyrobená z kompozitu založeného na termoplastoch, v ktorých bolo integrované tkanie dvoch vlákien, ľanu a čadiča, čo poskytne mechanickú pevnosť, ale aj lepšiu odolnosť voči vlhkosti.“
Ľan je získaný zo severného Francúzska, kde už je prítomný celý priemyselný ekosystém. Čadič je získavaný inde v Európe a je tkaný priemyselným partnerom INES. To znížilo uhlíkovú stopu o 75 gramov CO2 na watt, v porovnaní s referenčným modulom rovnakého výkonu. Hmotnosť bola tiež optimalizovaná a je menšia ako 5 kilogramov na meter štvorcový.
„Tento modul je zameraný na strešnú PV a integráciu budov,“ povedal Derrier. „Výhodou je, že má prirodzene čiernu farbu, bez potreby zákulisia. Pokiaľ ide o recykláciu, vďaka termoplastom, ktoré je možné prehodnotiť, je oddelenie vrstiev tiež technicky jednoduchšie. “
Modul je možné vyrobiť bez prispôsobenia prúdových procesov. Derrier uviedol, že myšlienkou je preniesť technológiu na výrobcov bez ďalších investícií.
„Jediným imperatívom je mať mrazničky na uloženie materiálu a nezačať proces zosieťovania živicí, ale väčšina výrobcov dnes používa Prepreg a je na to vybavená,“ uviedla.
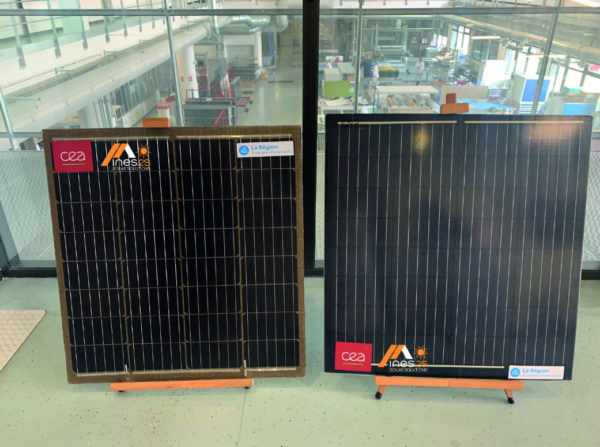
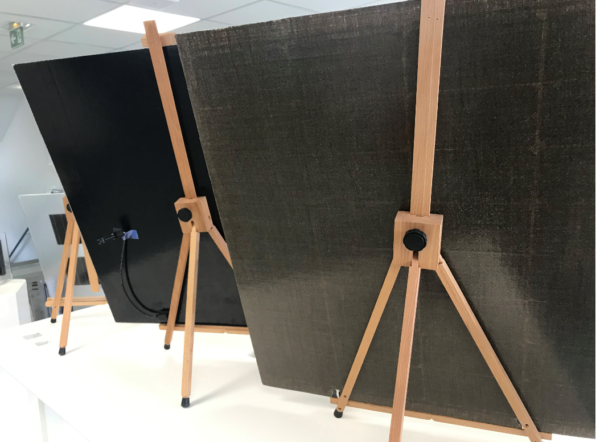
"Pracovali sme na druhom živote skla a vyvinuli sme modul zložený z opätovného použitého skla 2,8 mm, ktorý pochádza zo starého modulu," uviedol Derrier. „Použili sme tiež termoplastický enkapsulant, ktorý nevyžaduje zosieťovanie, ktoré sa preto bude ľahko recyklovať, a termoplastický kompozit s ľanovým vláknom pre rezistenciu.“
Zadná strana modulu bez čadiča má prirodzenú farbu bielizne, ktorá by mohla byť esteticky zaujímavá pre architektov napríklad z hľadiska integrácie fasády. Okrem toho nástroj na výpočet INES vykazoval 10% zníženie uhlíkovej stopy.
"Teraz je nevyhnutné spochybniť fotovoltaické dodávateľské reťazce," uviedol Jouini. „S pomocou regiónu Rhône-Alpes v rámci Medzinárodného plánu rozvoja sme preto hľadali hráčov mimo solárneho sektora, aby našli nové termoplasty a nové vlákna. Tiež sme premýšľali o súčasnom procese laminácie, ktorý je veľmi náročný na energiu. “
Medzi tlakom, stlačením a fázou chladenia laminácia zvyčajne trvá medzi 30 a 35 minútami, s prevádzkovou teplotou okolo 150 ° C až 160 ° C.
„Ale pre moduly, ktoré čoraz viac začleňujú materiály navrhnuté ekologické materiály, je potrebné transformovať termoplasty okolo 200 ° C až 250 ° C, s vedomím, že technológia HTJ je citlivá na teplo a nesmie prekročiť 200 ° C,“ uviedol Derrier.
Výskumný inštitút sa spojí s francúzskym indukčným termokompresným špecialistom Roctoolom, aby sa skrátil časy cyklu a vytvoril tvary podľa potrieb zákazníkov. Spoločne vyvinuli modul s zadnou tvárou vyrobenou z termoplastického kompozitu typu polypropylén, do ktorého boli integrované recyklované uhlíkové vlákna. Predná strana je vyrobená z termoplastov a sklenených vlákien.
"Indukčný termokompresný proces spoločnosti Roctool umožňuje rýchlo zahriať dve predné a zadné platne bez toho, aby musel dosiahnuť 200 ° C v jadre buniek HTJ," uviedol Derrier.
Spoločnosť tvrdí, že investícia je nižšia a proces by mohol dosiahnuť čas cyklu iba niekoľko minút, pričom využíva menšiu energiu. Táto technológia je zameraná na kompozitných výrobcov, aby im poskytla možnosť vyrábať časti rôznych tvarov a veľkostí a zároveň integrovať ľahšie a odolnejšie materiály.
Čas príspevku: jún-24-2022