Francúzsky inštitút pre solárnu energiu INES vyvinul nové fotovoltaické moduly s termoplastmi a prírodnými vláknami pochádzajúcimi z Európy, ako je ľan a čadič.Cieľom vedcov je znížiť ekologickú stopu a hmotnosť solárnych panelov a zároveň zlepšiť recykláciu.
Panel z recyklovaného skla na prednej strane a ľanový kompozit na zadnej strane
Obrázok: GD
Z časopisu pv France
Výskumníci z francúzskeho Národného inštitútu pre solárnu energiu (INES) – divízie Francúzskej komisie pre alternatívne energie a atómovú energiu (CEA) – vyvíjajú solárne moduly s novými biologickými materiálmi na prednej a zadnej strane.
„Keďže uhlíková stopa a analýza životného cyklu sa stali základnými kritériami pri výbere fotovoltaických panelov, získavanie materiálov sa v najbližších rokoch stane v Európe kľúčovým prvkom,“ povedal Anis Fouini, riaditeľ CEA-INES. , v rozhovore pre pv magazín France.
Aude Derrier, koordinátorka výskumného projektu, uviedla, že jej kolegovia sa pozreli na rôzne materiály, ktoré už existujú, aby našli taký, ktorý by umožnil výrobcom modulov vyrábať panely, ktoré zlepšujú výkon, odolnosť a náklady a zároveň znižujú dopad na životné prostredie.Prvý demonštrátor pozostáva z heterojunkčných (HTJ) solárnych článkov integrovaných do celokompozitného materiálu.
"Predná strana je vyrobená z polyméru naplneného sklenenými vláknami, ktorý poskytuje transparentnosť," povedal Derrier.„Zadná strana je vyrobená z kompozitu na báze termoplastov, do ktorého je integrovaná väzba dvoch vlákien, ľanu a čadiča, čo zabezpečí mechanickú pevnosť, ale aj lepšiu odolnosť voči vlhkosti.“
Ľan pochádza zo severného Francúzska, kde sa už nachádza celý priemyselný ekosystém.Čadič sa získava inde v Európe a je tkaný priemyselným partnerom INES.To znížilo uhlíkovú stopu o 75 gramov CO2 na watt v porovnaní s referenčným modulom s rovnakým výkonom.Hmotnosť bola tiež optimalizovaná a je necelých 5 kilogramov na meter štvorcový.
„Tento modul je zameraný na strešnú fotovoltaickú energiu a integráciu budov,“ povedal Derrier.„Výhodou je, že je prirodzene čiernej farby, bez potreby rubovej vrstvy.Čo sa týka recyklácie, vďaka termoplastom, ktoré je možné pretaviť, je oddelenie vrstiev aj technicky jednoduchšie.“
Modul je možné vytvoriť bez prispôsobenia súčasných procesov.Derrier povedal, že myšlienkou je preniesť technológiu na výrobcov bez ďalších investícií.
„Jediným imperatívom je mať mrazničky na skladovanie materiálu a nezačínať proces sieťovania živice, ale väčšina výrobcov dnes používa predimpregnované lamináty a sú už na to vybavené,“ povedala.
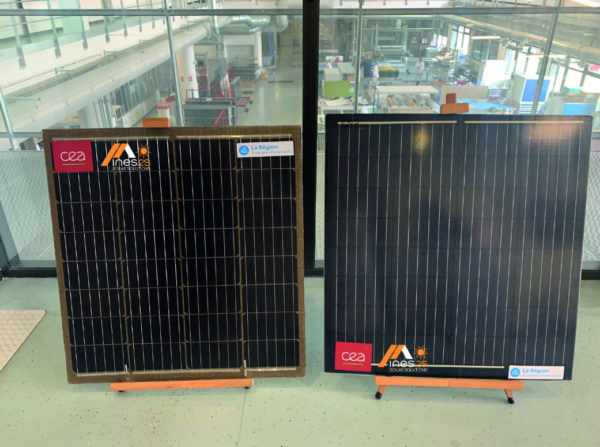
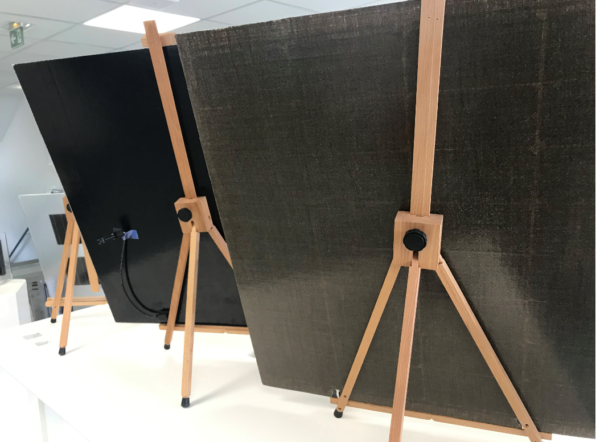
„Pracovali sme na druhom živote skla a vyvinuli sme modul vyrobený z opätovne použitého 2,8 mm skla, ktoré pochádza zo starého modulu,“ povedal Derrier.„Použili sme aj termoplastickú zapuzdrenú látku, ktorá nevyžaduje zosieťovanie, a preto sa bude dať ľahko recyklovať, a termoplastický kompozit s ľanovým vláknom pre odolnosť.“
Zadné čelo modulu bez čadiča má prirodzenú farbu ľanu, čo by mohlo byť pre architektov esteticky zaujímavé napríklad z hľadiska integrácie fasády.Okrem toho výpočtový nástroj INES ukázal 10 % zníženie uhlíkovej stopy.
"Teraz je nevyhnutné spochybniť fotovoltaické dodávateľské reťazce," povedal Jouini.„S pomocou regiónu Rhône-Alpes v rámci Medzinárodného plánu rozvoja sme preto hľadali hráčov mimo solárneho sektora, aby sme našli nové termoplasty a nové vlákna.Mysleli sme aj na súčasný proces laminácie, ktorý je veľmi energeticky náročný.“
Medzi fázou natlakovania, lisovania a ochladzovania trvá laminovanie zvyčajne 30 až 35 minút pri prevádzkovej teplote okolo 150 C až 160 C.
"Ale pre moduly, ktoré čoraz viac obsahujú ekologicky navrhnuté materiály, je potrebné transformovať termoplasty pri teplote okolo 200 °C až 250 °C s vedomím, že technológia HTJ je citlivá na teplo a nesmie prekročiť 200 °C,“ povedal Derrier.
Výskumný ústav sa spojil s francúzskym špecialistom na indukčnú termokompresiu Roctool s cieľom skrátiť časy cyklu a vytvoriť tvary podľa potrieb zákazníkov.Spoločne vyvinuli modul so zadným čelom z termoplastického kompozitu polypropylénového typu, do ktorého boli integrované recyklované uhlíkové vlákna.Predná strana je vyrobená z termoplastu a sklolaminátu.
„Indukčný termokompresný proces spoločnosti Roctool umožňuje rýchlo zahriať dve predné a zadné platne bez toho, aby bolo potrebné dosiahnuť 200 °C v jadre článkov HTJ,“ povedal Derrier.
Spoločnosť tvrdí, že investícia je nižšia a proces by mohol dosiahnuť čas cyklu len niekoľko minút pri nižšej spotrebe energie.Táto technológia je zameraná na výrobcov kompozitov, aby im umožnila vyrábať diely rôznych tvarov a veľkostí a zároveň integrovať ľahšie a odolnejšie materiály.
Čas odoslania: 24. júna 2022